SUCCESS STORY
Fortune 500 Automotive Supplier Reduces Production Downtime
Customer
The leading Tier 1 automotive supplier from the USA is known for its extensive global production network and the important role it plays in the supply chain for OEMs worldwide. With state-of-the-art manufacturing facilities on several continents, the supplier is a core partner for automotive manufacturers around the globe.
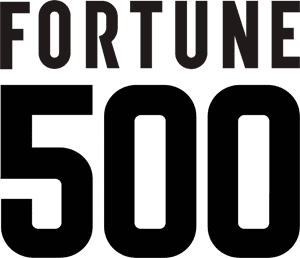
Challenge: Inefficiencies in the Value Chain
Manual processes between individual production steps of the value chain not only led to costly errors and inefficient processes, but also to unplanned downtimes along the production lines. Among other things, the tedious manual booking of materials in the ERP system and the release of production steps after quality checks were symptomatic of the existing bottlenecks.
Solution: Process Automation with i-flow
To automate the processes, the customer chose the Industrial Unified Namespace (UNS) from i-flow. In just a few months, the customer has connected 60+ systems (e.g., PLCs, databases, SAP, AWS) and automated over 20 million operations daily with the i-flow software. As a result, material flows are now synced with SAP in real-time, production-critical data is shared with OEMs via the cloud, and production steps are released automatically based on prior quality checks.
For security reasons, the customer assigned individual permissions (e.g. write / read) to the various user groups (several OT groups + IT) to essentially manage access to individual systems (e.g. SAP reads, PLC writes). This prevents non-authorized users from writing to production-critical systems.
“i-flow is more powerful every time.”
– Lead Architect Smart Manufacturing
Benefits: Minimizing Unplanned Downtimes
The implementation of i-flow led to considerable benefits and a significant increase in efficiency. By automating processes, productivity was increased by 8% (in direct production and indirect office areas). Manual errors were eliminated, minimizing unplanned production downtime by 38% and significantly increasing plant OEE.
DOWNLOAD FULL SUCCESS STORY
Was does the Fortune 500 do?
- Tier 1 automotive supplier
- production facilities on several continents
Challenge
- manual processes
- unplanned downtimes
Solution
- IT/OT integration with i-flow
- process automation via Microservices
Benefits
- -38% unplanned downtimes
- +8% productivity
“The successful implementation of i-flow illustrates the enormous potential of process automation at the interface between IT and OT. Thanks to flexible and scalable IT/OT system integration, we were able to optimize our processes and increase competitiveness.”
Lead Architect Smart Manufacturing
400 Mio. Data Operations per Day
Over 400 million data operations per day in production-critical environments demonstrate the scalability of the software and the deep trust that customers place in i-flow.
Whether PLC, sensor or ERP data, i-flow provides the basis for a modern IT/OT architecture in manufacturing companies.
i-flow Operations this month: -
Over 400 million data operations per day in production-critical environments demonstrate the scalability of the software and the deep trust that customers place in i-flow.