SUCCESS STORY
Hirschvogel Group: Increasing Line Output
Customer
The Hirschvogel Group is a leading manufacturer of steel and aluminum components. The company focuses on innovation in product design and manufacturing technology and is known for its high level of vertical integration and quality. With 8 production sites and around 6,200 employees worldwide, Hirschvogel is one of the most important automotive suppliers.
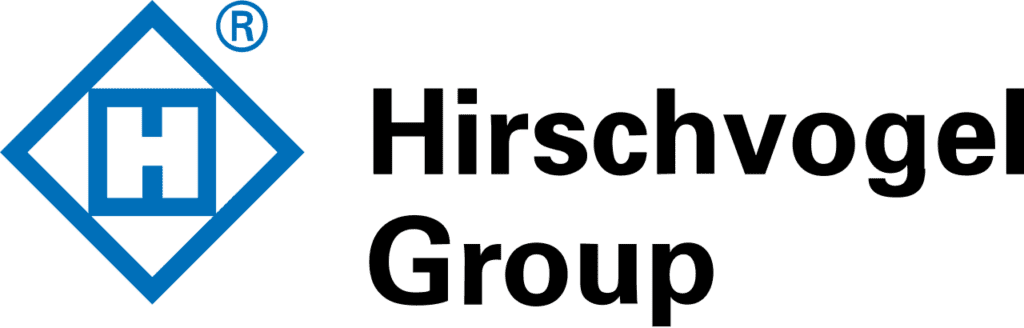
Challenge: Line Performance and Scalability
The Hirschvogel Group is facing major challenges in implementing its vision of a smart factory. A complex IT/OT architecture, silos and a lack of standards at the production sites represented significant structural hurdles. These include:
- Complex IT/OT architecture limits line performance and scalability
- IT/OT data silos make it difficult to access data
- Lack of standards compromises data quality and scalability
Solution: i-flow's High-Performance Data Infrastructure
Hirschvogel Group uses i-flow’s Industrial Unified Namespace (UNS) as its central data hub. The UNS of i-flow creates a high-performance, high-availability data infrastructure in the productions sites worldwide and lays the foundation for realizing the smart factory vision.
The implementation was done in 2 steps:
- Realtime control of production lines: Implementation of the i-flow Edge for real-time control of production lines. The aim was to minimize the latency of production control data streams in order to increase line output. In order to guarantee continuous production operations, it was essential to ensure a high-availabliblity infrastructure through redundant i-flow setups.
- Central IT/OT interface: Implementation of the i-flow Broker as a central interface between IT and OT systems. The aim is to break down silos and maximize the availability and quality of data. With its 1:n integration between OT and IT systems, the UNS from i-flow becomes the central data hub for the Hirschvogel Group. This simplifies the implementation and scaling of smart factory use-cases.
“The i-flow software offers the fastest communication times between machine controllers and IT systems and is the most scalable and comprehensive solution we have tested on the market.”
– Philipp Steuer (IT Administrator)Why i-flow?
The strategic decision in favor of i-flow’s Industrial Unified Namespace (UNS) was based on a comprehensive market evaluation. The following factors, among others, played a key role:
- High-Performance Solution: i-flow offers a modular infrastructure that is designed for maximum performance and realtime data processing.
- Outstanding Customer Service: i-flow is an outstanding customer-oriented company with fast support and short response times.
- Scalability and User-Friendliness: i-flow combines a highly intuitive software for quick payoffs with the ability to scale easily.
“Working with i-flow sets new standards: the team impresses with its deep technical understanding and first-class customer support. i-flow combines highly intuitive software that enables quick wins with the ability to scale easily.”
– Dominik Malek (Program Lead Smart Factory)
Benefits: Increase in Line Output
Thanks to i-flow, the Hirschvogel Group was able to implement an open, event-based and scalable architecture that ensures the long-term flexibility and future readiness of the company and provides the foundation for realizing the Smart Factory vision.
The advantages in detail:
- Increase in Line Output: Increase in line output by reducing latencies of production control data streams by 88 %.
- Rapid Rollout: Successfully installed in several factories, i-flow connects dozens of machines and processes over 4.2 million messages every day (growing strongly).
- Foundation for the Digital Transformation: Implementation of a central access point for IT/OT data and events based on an open, event-based and scalable architecture.
DOWNLOAD FULL SUCCESS STORY
What does Hirschvogel do?
- Leading automotive supplier
- 6200 employees worldwide
Challenge
- Complex IT/OT architecture
- Lack of standards compromises data quality and scalability
Solution
- Realtime control of production lines
- i-flow as a central IT/OT interface
- 4.2 million messages/day (growing strongly)
Benefits
- Increase in line output
- Foundation for Smart Factory vision
"We are proud to boost the competitiveness of Hirschvogel on the basis of i-flow technology and to create the foundation for the customer's vision of the smart factory. Hirschvogel impressively demonstrates how the use of our high-performance and highly scalable data infrastructure lays the foundation for future-oriented production."
Daniel Goldeband (Director, i-flow GmbH)
400 Mio. Data Operations per Day
Over 400 million data operations per day in production-critical environments demonstrate the scalability of the software and the deep trust that customers place in i-flow.
Whether PLC, sensor or ERP data, i-flow provides the basis for a modern IT/OT architecture in manufacturing companies.
i-flow Operations this month: -
Over 400 million data operations per day in production-critical environments demonstrate the scalability of the software and the deep trust that customers place in i-flow.